The first Flexo type printing presses were patented in the late 19th century. Originally, flexographic printing was rudimentary in quality with its limitations in ink control and rubber printing plates. Commercial print applications were open to all but the most basic of print & packaging products. As the consumer industry grew, packaging & labels requiring high-quality print were generally being produced using the offset & letterpress processes until more recently. Since 1990, great advances have been made to the quality of flexographic printing presses, printing plates, printing units, drying systems & inks. These advances have combined to rival offset quality with improved practicality, higher production speeds, and lower capital investment.
The greatest advances in flexographic printing have been in the area of photopolymer printing plates, the plate material and the method of plate creation. Companies like Asahi Photoproducts, AV Flexologic, Dupont, MacDermid, BASF & TOK have pioneered the latest technologies, with advances in faster processing, washout and the latest reprographic screening techniques to reproduce high tonal values . This has allowed Flexo to grow & dominate production in the many print sectors such as labels & packaging and even move into new applications such as cartons.
Recently, digital direct to plate systems support greater improvements in image reproduction, reducing the turnaround time from a computer to proofing, to press.
Laser-etched ceramic anilox rolls also play a part in the improvement of print quality through the ability to control Ink volume transfer. Full-color picture printing is now possible, and some of the finer presses available today, in combination with a skilled operator, allow quality that rivals the lithographic process. One ongoing improvement has been the increasing ability to reproduce highlight tonal values, thereby providing a workaround for the very high dot gain associated with flexographic printing.
Printing Presses have evolved alongside those advances already discussed in other areas of the process. A modern press today should offer a stable platform with servo or precision gearbox mechanical drives and digital control systems. Automated functions & closed loop digital controls mean that print quality provided is less dependent on a highly skilled machine operator. Press manufacturers are ensuring their machines are easier to set up & run, reducing waste and improving production capacity. Even a combination of print processes such as flexo,offset, foiling & digital is allowing the print packaging designer a wealth of new opportunities to stand out from the crowd.
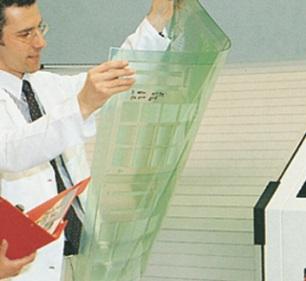
Reprographics:
The power of computers & graphics programs has transformed printing in general. Reprographics is a blanket term encompassing multiple methods of reproducing content, such as scanning , photography, photocopying and analogue printing & digital printing. The term applies to both physical and digital reproductions of documents and images. Supplied with artwork, a number of stages have to be processed in order to get the image to a print ready format. What was a very skilled and time-consuming stage has now been automated across all print disciplines. Some regularly used terms are discussed here.
1) Trapping:
Is defined as the compensation of the size of adjacent images to allow for registration errors. Trapping allows a certain overlapping tolerance when two colours meet and helps to eliminate these problems. It usually involves expanding the lighter of the two colours to overlap into the darker colour, which should hold the overall shape of the image or text. Sometimes, gaps are left to prevent two colours mixing.
2) Step & Repeat:
Is the action of reproducing a number of label design images onto film and subsequently plate, so that it can be printed as more than one label at a time. This can considerably reduce press running time and the amount of material used. This process is now done through industry specific software but was traditionally a very skilled and complicated process.
3) Dot Gain Compensation:
Dot gain is a normal printing characteristic or defect in which the size of a half-tone dot changes as a result of platemaking and printing. For example, letterpress and flexo dots print larger on a softer material than they do on a harder film surface. This, in turn, has the effect of darkening the colour or tone of the printed image as the ink is now spread over a greater area than originally intended. Compensation for dot gain can be accommodated at the reprographic stage and is based upon plate material and substrate together with specific press information. Typically, a press fingerprinting analysis is undertaken on all new presses to determine the registration, dot gain, distortion and other characteristics of the press. This press information is vital and is used to minimize dot gain and make it predictable thus ensuring consistent, high-quality print.
4) Colour Separation:
For plate production, separation is the term used to describe the process of converting an image, such as a photograph, into a set of colours that can be printed. Full-colour printing uses the four ink colours, cyan, magenta, yellow, and black (CMYK). These colours are printed separately but on top of one another to reproduce literally millions of different colours and shades.
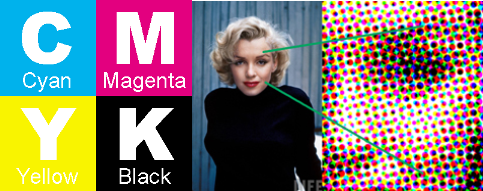
Water & Solvent vs Digital Printing Plates & Laser Engraved Rolls
The most common imaging systems in use for flexo printing plates today are analog and digital direct to plate systems. For the analog system, the matt film/negative is imaged separately and then applied to the surface of an analog plate, covered with a vacuum sheet, and, with vacuum applied, exposed to the UV light. The final dots and lines on the plate are enlarged to some extent compared to dots and lines on the film, due to the deflection and refraction of light passing through the cover sheet, the imaged film, and the plate slip cover that stops the film sticking to the photopolymer. An analog plate has a flat top dot structure with a good support structure, for excellent on-press performance.
Digital plates do not use a film/negative, but instead, a black layer is applied to the surface of the plate. The black layer is then ablated using a high power laser imaging device, removing the black layer where image areas are required, and leaving the rest to be the mask for the non-image areas. The plate is then exposed in a normal exposure unit, but without the vacuum—meaning it is exposed in the presence of air. The oxygen in the air reacts with the photo initiators, slowing the polymerization process, resulting in shrinkage of the dots and instead of flat tops, they are bullet shaped dots.
A fourth platemaking method is direct laser engraving where the unwanted areas are ablated by very high-powered lasers, leaving the image areas behind. This is the only truly digital imaging processing of flexo printing rolls, not relying on further chemical reactions with UV exposure, and plate processing. It is typically used for continuous print roll image and sleeve imaging applications. Speed and costs of the laser systems are the greatest current limitations to growth of this process.
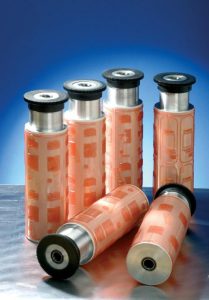
Platemaking Systems Overview
Flexo platemaking, in its most basic concept, is very simple. You start with a sheet of solid material, selectively alter it chemically using UV light, then remove the areas you don’t want, leaving the areas you do want as the image. More than 30 years ago flexo plates were made by hand, carved out by skilled plate makers but they really did equate in many ways to sophisticated “potato printing” and gained flexo its low print quality reputation. But, today it is very different, increasingly scientific, and significantly better.
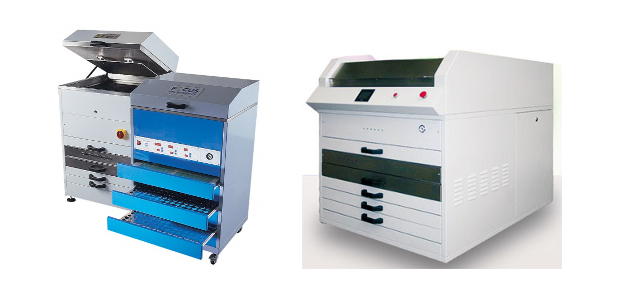
Analog platemaking systems
When manufacturing a plate, the raised image area is a distance above the polymer base, which is called the floor. The height from the floor to the image area surface is the plate relief. The back of the plate is supported by a film layer to provide dimensional stability.
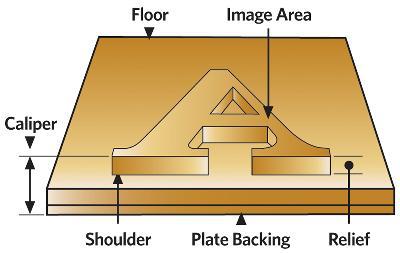
Normally the first step is to expose the back of the plate to UV light, curing it evenly to build and raise the plate floor to its required level. This also activates the monomers and photo-initiators throughout the rest of the photopolymer mass.
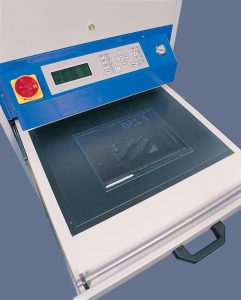
The areas of unpolymerized photopolymer are then removed—using a variety of methods—to the plate floor leaving the image area behind. The most common methods for removing the non-image area on sheet plates involve either washing it away with plate washout chemistries (traditional solvents, new low-odor plate processing solutions, or water and detergent combinations) or a thermal process (involving heat to melt the polymer, and remove it with a wicking material under pressure).
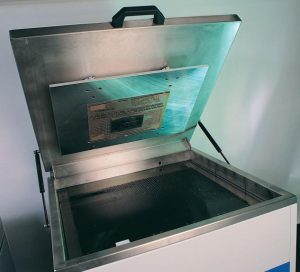
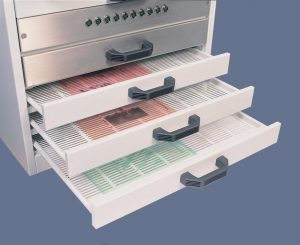
The plate is then ready for inspection, measurement, and finishing. The plate should be allowed to stand for a period before use because the chemical reactions of photopolymerization do not stop immediately, but often continue several hours after exposure to the UV light, until the plate is fully stabilized. Running the plate on-press too soon risks shortening the plate life and affecting stability, especially in fine details.
This is the basic explanation of platemaking, and is relatively simple. What makes platemaking more complex is the huge variety of possible combinations of photopolymer plate materials, plate thicknesses, plate hardness, mask and imaging technologies, plate processing systems, plate processing solutions, and finishing options. These also depend on the final application for the plates, whether narrow-web labels, carton board, envelopes, wide-web films, multiwall bags, or corrugated, to name just a few.
A Few More Details
Plate Exposure
A critical step in all flexo platemaking is the exposure of the plate to UV light to cause the chemical reaction for the polymerization of the image areas. This is a critical step in the control of the final plate produced. The basic technology for this has changed very little in the last 20 years, with small incremental steps, rather than major steps, forward. The key to the process is consistency and repeatability.
It is known that variables such as heat and humidity can affect the process and the final result. Simple items like a chilled bed of the exposure table, and sufficient airflow to remove the air heated above the plate can greatly enhance the consistency. Also to address the natural tendency of the UV tubes to lose intensity and power over time, the inclusion of a light integrator that measures the light output and adjusts the exposure time automatically to ensure consistent light energy is an important feature on a modern plate processing system.
Plate Processing
For all flexo platemaking except direct laser engraving, the processing of the plate is a chemical process. The unwanted monomers and photo initiators are dissolved or melted and then removed. The most common plate processing methods use a plate washout chemistry—either water and detergents as a water wash solution or solvents as a solvent washout system. In both cases, the washout chemistries absorb the unwanted photopolymer, but can be recycled and removed, by separating and removing the unwanted photopolymers, which are sent for safe disposal, often through incineration.
Washout Solution
The solvents used today are available with no reportable hazardous components, low odor, reduced VOC levels, and an operator-friendly nature. They are recovered using traditional distillation, or cold recycling systems, with 1 gallon of solvent recovered at about a 90 percent rate each time, and capable of producing approximately 40 square feet of 0.067˝ photopolymer plates per gallon, before being completely exhausted.
The choice of solvent wash, water wash, or thermal plate & digital processing should be a decision based on technical requirements. Consider each process’s distinct benefits and drawbacks, e.g. solvent plate processing being capable of producing plates to the highest specifications, but thermal processing being the most convenient and faster today. Keep in mind that new chemistries and cold recycling systems are changing this balance in terms of speed and convenience.
The Next Steps
If after reading this e-book you’d like to discuss any of the issues raised, or have any questions about our products or services, please do not hesitate to get in touch with a member of our experienced customer service team. We hope you found this guide useful and informative, and we look forward to speaking to you in person.
To find out more, give us a call on 01949 836 223 or send us an email to admin@focuslabel.com
Other related documents & ebooks (available on request)
Anilox Roll Technology: Textile Printing Inks: Printing Plates: Drying Systems : Heat Transfers