One reason for the comparatively slow growth of digital printing on textiles may be related to the extreme demands of the textile applications and the wide selection of types of textiles used in the industry. Fabric has always been inherently more difficult to print due to its flexible nature. The level of flexibility varies from warp to weft and with each degree around the bias, so guiding the fabric precisely through a digital printing press has proven to be very difficult, not forgetting the challenges of softness, fading, rub and wash resistance.
Digital textile printing is described as method of printing colorants onto fabric. Most notably, digital Ink Jet textile printing is referred to when identifying either printing smaller designs onto garments (T-shirts, dresses, promotional wear; abbreviated as DTG, which stands for Direct to Garment) and printing larger designs onto large format rolls of textile. The latter is a growing trend in visual communication, where advertisement and corporate branding is printed onto polyester media. Examples are: promotional & lightweight sports apparel flags, banners, signs, retail graphics.
![]() |
Types Of Printing Can Be Divided Into:
|
Multi Pass Scan Or Single Pass Inkjet
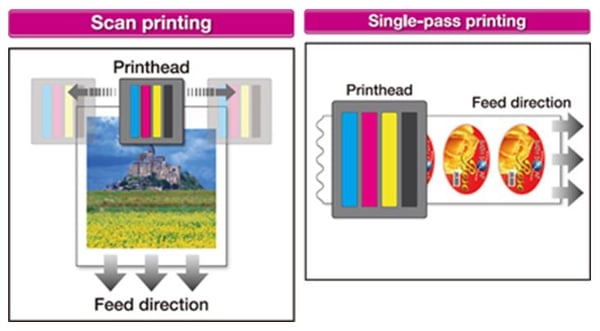
For printing of wide textiles multi pass scan printing is well established, operating ina similar way to your desk top printer at home. These scanning printing systems are relatively low cost compared to a single pass print engine. But multi pass systems are relatively slow and restricted to production speeds of a few metres per minute. Single pass systems are very fast with printing speeds ranging from 20 to 80 Mts per min. There are no moving parts in a single pass printing head, only the web is moving , transported below the print head. For this reason the wider the print width the higher cost of the print engine as it will use more print heads than a scanning system
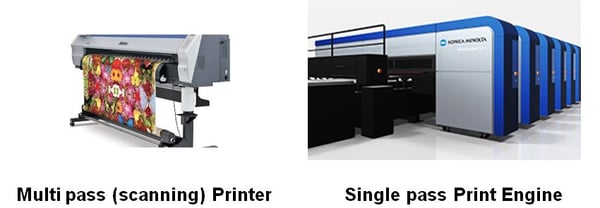
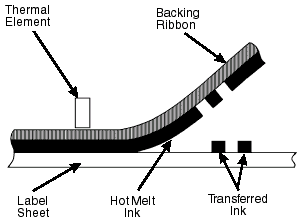
Digital Printing Labels For Garment/Apparel
There are a number of digital printing technologies currently used for garment labelling & branding. The most common system is a development of analogue hot foil stamping. The digital development uses thermal transfer properties to melt a coloured foil and transfer is directly to the textile ribbon so it becomes fixed. The heated platen/print head is programmed to produce an image as the textile Ribbon & ink foil pass under the print head. However, it is relatively slow and expensive, as much as 90% of the special foil is wasted. These systems are mainly used within ‘In house’ garment producers for their own labelling applications.
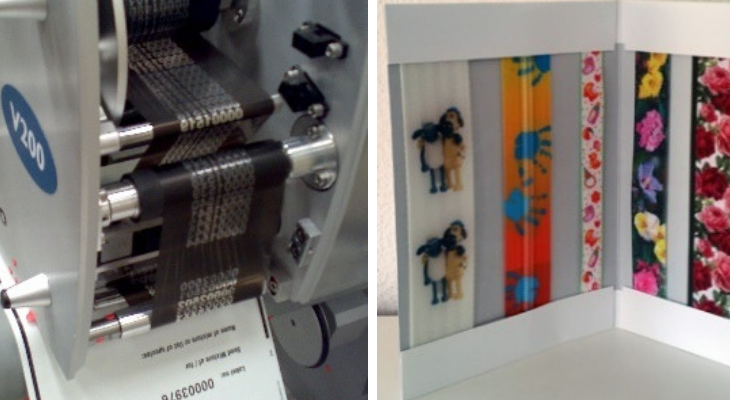
Recently we have seen special scan printers adapted & used for direct CMYK printing of elastics & ribbons from the likes of market leading textile machinery producer Jakob Muller. The limitations on scan printers can easily be seen in speed, but also limitations in using dye sublimation inks which is only printable on polyester products reduces choice of fabric type. Despite this the results are excellent and deserve serious consideration for those in that line of business.
For this remainder of this article we are going to concentrate on single pass Ink Jet technology for printed garment label applications, narrow web ribbons & elastics. Digital ‘Ink jet’ is the latest technology to present the possibilities for higher volume output more in line with analogue printing, providing the flexibility & advantages of digital printing with the durability and economies of volume production. As with analogue printing the ink used is the only consumable, but without the added cost of printing Plates or Screens.
Focus has been supplying digital print engines & hybrid flexo machines within the packaging industry for several years and has taken its expertise in analoge printing for garment labels & ribbons and integrated the digital technology from its packaging sector equipment.
The modular nature of digital print heads makes it a perfect match for narrow ribbon printing using single pass technology. It has allowed us to strip the engine components down to produce an affordable single pass solution for this niche market. The powerful graphics software is tailored towards textiles with CMYK colour management system allowing greater control of ink processing across a range of textiles, with ability to process & print complex graphics, variable information relative to sizes, composition, store codes, dates etc ,without stopping the press.
Available printing widths are 72, 145 or 212mm in full process CMYK colour printing, spot colour or mono print options with printing on both sides of the ribbon. We offer special Infra-red or UV drying options, subject to Ink type used. Developments on new inks continue, however in the main they are pigment based in order to cover as many textile applications as possible. Some pre & post print treatments may be required.
Let’s be clear that digital printing technology is an sizeable investment needing careful consideration , machines are high value, digital Inks are more expensive than analogue inks, textile ribbons may require special pre-treatment & post treatments before the label is ready to deliver to the end client, but this all has to be factored against huge benefits.The traditional industry still looks at digital textile printing parameters from the context of what it “can’t do,” compared to conventional printing. Conversely there are many things conventional print cannot do compared to Ink jet.It is true the presently digital is a new technology and does have some limitations so let us concentrate on what Ink jet printing can do.
What Can Digital Ink Jet Do For Me?
- Minimal set up costs – short runs and samples are economical – Costs per print are the same for 1 or 10,000.
- There is no down time for set up – the printer is always ready to print – so there is also increased productivity.
- Unlimited repeat length
- No Screens
- No Printing plates
- Continuous printed images (no gap)
- Variable Information printing including Bar code & QR codes are possible.
- Job Que for economic production.
- Instant size changes.
- Faster turnaround time – and very fast design changes. Turnaround time for samples can be reduced from several days to a few hours.
- Print on demand, dramatically reducing time to market.
- Just-in-time customization or personalization
- Lower energy cost
- Smaller production area
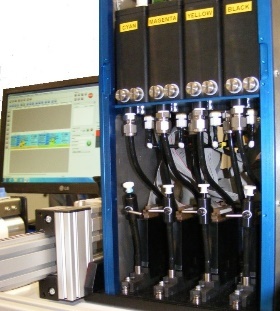
Now For The Challenges
- There are many types of Ribbons used in garment labelling applications. combinations of synthetic and natural fibers, each with its own ink compatibility characteristics (one ink does not fit all & pre-testing is always recommended)
- In addition to dealing with a fabric that is stretchable and flexible, it is often a highly porous and textured surface (additional Finishing /Pre-coating may be required to present a printable surface for this process)
- End user requirements include light fastness, water & wash fastness (sweat, too) through finishing operations and often outdoor use, heavy wear, abrasion, and cleaning (post treatment may be required to meet specific performance characteristics)
- The label not only has to look & feel good, but the information printed must be legible and withstand up to 50 washing cycles or the lifetime of the garment. (again post treatments may be required to achieve wash resistance targets)
- Fabric has much greater absorbency, requiring many times the ink volume compared with printing on papers. (pre-coating or finishing may be required)
- Before any printing is carried out, the designs need to be developed in a digital format that can be read by the print engine.
- Safety standards: Inks, fabrics & additional processes must pass strict safety tests for application in within garments or any skin contact application.
- Limited Colour pallet to CMYK plus one or two spot colours. Whilst this is the case CMYK will cover 80% of the pantone range & corporate colours. Fortunately the majority label printing does not require a wide range, and colours are often limited to just black & red.
In the face of such odds, digital textile printing is happening. And how! Digital inkjet printing has become one of the most important textile production printing technologies and is, in fact, transforming the industry and will continue to grow. All future development has to be based on co-operation between the design & graphics software companies, the ink manufacturers, the fabric/ribbon manufacturers and the printing machine developers. If you want to take a step into the digital revolution contact focus today or arrange an appointment to discuss the possibilities.